Exploring 12 Common Sensor Types & Their Impact on Performance, Safety, & Convenience From kitchen appliances to vehicles, electronic sensors have long been essential components inside the devices we enjoy as a society. Sensors are used to detect...
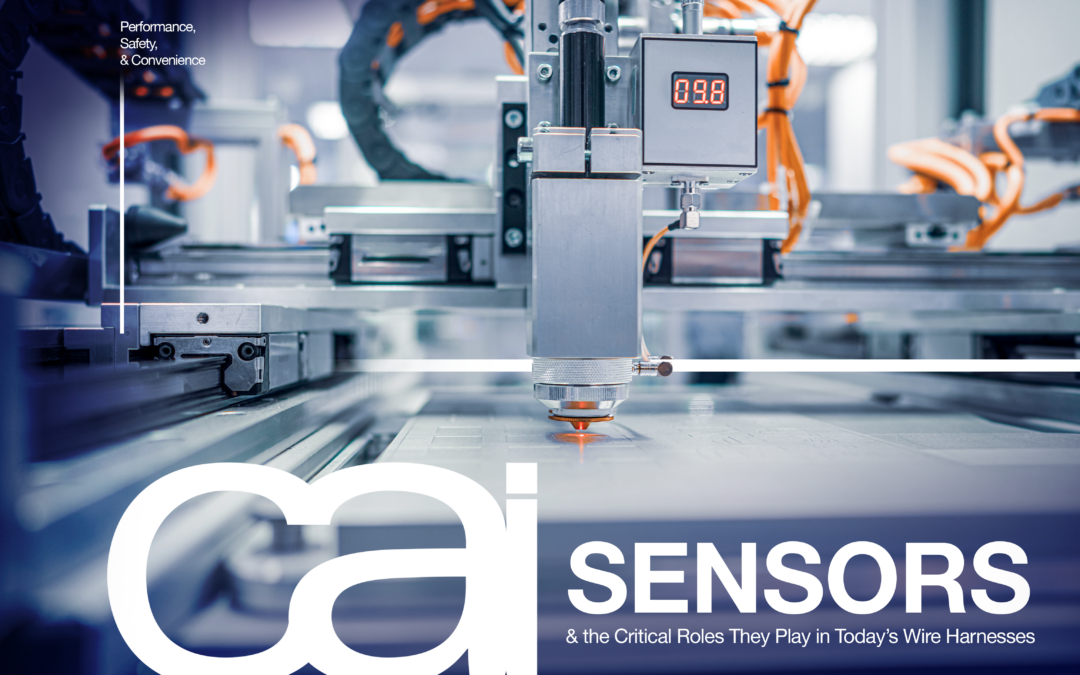
Exploring 12 Common Sensor Types & Their Impact on Performance, Safety, & Convenience From kitchen appliances to vehicles, electronic sensors have long been essential components inside the devices we enjoy as a society. Sensors are used to detect...
Why CAI is Your Wire Harness Cost Savings Solution In the increasingly competitive world of modern manufacturing, wire harnesses are essential components across a broad range of industries, from automotive and aerospace to industrial machinery and consumer...
Intricate Wire Harnesses Require Custom Solutions From Trusted Experts Used in countless electrical applications, wire harnesses come in all shapes, sizes, and complexities. While a “simple” wire harness organizes a handful of wires into a bundle for basic...
Ensuring Optimal Safety in Wire Harness Design The ability to control and utilize electricity — for everything from lighting homes to powering cars — is easily one of history’s greatest achievements, leading to many of our modern conveniences. However, there...
Extreme Conditions Call for Extra Consideration in Wire Harness Manufacturing Wire harnesses must be carefully crafted in order to effectively supply power and data to the machines and devices we use in our homes and businesses every day. The same is true for...
Electrical cables and wires are all around us, whether inside the buildings we occupy, buried deep in the ground, or stretched across pools high above. Because they’re used for a wide variety of applications and environments, they must be able to endure varying conditions and threats, including extreme temperatures, chemicals, vibrations, and more. Maybe the most significant threat that electrical cables and wires face is water.
Because non-pure water (which is most of the water we encounter) is a highly effective conductor of electricity, it can easily disturb the flow of electricity when coming into contact with a damaged or poorly constructed conductor (i.e. wire or cable). What can happen when water infiltrates a cable or wire and its protective barriers?
By affecting the flow of electricity and the power and signals that come with it, water can lead to electrical malfunctions like short circuits, power outages, and device failure
When moisture contacts a conductor, it can cause sparks, arcing, or overheating that can ignite nearby combustible materials, which can damage property and endanger lives.
Water can redirect electrical current from a conductor into the body of someone touching the electrified water. The resulting electric shock can cause serious injury, from burns and heart failure to nerve damage and even death.
An electrical cable is a sheathed conductor or bundle of conductors used to transmit electric power or signals from one point to another, often from one electrical device to another. A waterproof electrical cable, also known as a water-block cable or water-resistant cable, is a cable designed to operate effectively and reliably in environments where water can be a threat, and even be submerged in varying water types, temperatures, and depths.
Unique not only in construction but also in their installation and application, waterproof cables feature water-tight connectors and are created with special manufacturing processes to prevent water from damaging the materials or reaching the conductor in outdoor or underwater settings. Waterproof cables are utilized in nearly every industry for a wide variety of applications including fire alarm systems, military hardware, oil and gas refineries, outdoor audio-visual equipment, and marine communications.
Oftentimes, the design, testing, and manufacturing of a cable takes substantial time, money, and resources, no matter the volume. Fortunately, there are a number of high-quality off-the-shelf (OTS) cables and cable assemblies that can be customized and enhanced with special manufacturing processes to create highly reliable, water-resistant cable systems.
When creating waterproof cables, it’s vital to have experts involved in the process due to the critical safety and performance issues involved. After identifying the ideal off-the-shelf options to match volume needs and intended application, CAI applies overmolding to craft a custom cost-effective, ultra-reliable waterproof cable solution. Connect with us today!
Dusty and damp environments can wreak havoc on cables and wires when not properly protected. To ensure greater safety and performance from electrical products, the International Electrotechnical Commission (IEC) — the world’s leading organization for the preparation and publication of international standards for all electrical, electronic and related technologies — created the Ingress Protection (IP) rating.
Increasingly common for consumer and industrial electronic devices, machines, cabling, and wiring, the IP rating (as defined by IEC standard 60529) is a two-digit system that grades the resistance of an enclosure against the intrusion of dust and liquids. The first number (ranging from 0-6) corresponds to solid foreign particle protection while the second number (ranging from 0-9) corresponds to moisture/water protection. The higher the number, the greater the protection. IP-67 and IP-68 compliant cables are among the most common and reliable water-resistant cables.
0 – | No protection |
1 – | Protected against condensation & water droplets |
2 – | Protected against dripping water deflected up to 15° from vertical |
3 – | Protected against spray up to 60° from vertical |
4 – | Protected against water spray from all directions |
5 – | Protected against low-pressure water jets from all directions |
6 – | Protected against strong water jets and waves |
7 – | Protected against temporary immersion (up to 30 minutes) |
8 – | Protected against prolonged immersion under pressure |
9 – | Protected against powerful, high-temp spray at close range |
Waterproof cables are usually constructed with multiple levels of water protection, from inner isolation sleeves to outer jackets and overmolding. Polyvinyl chloride (PVC), polyethylene (PE), and high-density polyethylene (HDPE) are among the most common, reliable materials used for waterproofing.
Submersible cable systems are typically designed to be laterally and longitudinally watertight, through a variety of methods and materials such as water-blocking conductors, swellable tape, water-blocking rope, powder, yarn, tape, and gel. Laterally watertight protection helps prevent water from penetrating the cable when the sheathing is damaged, while longitudinally watertight cable features a barrier to spread moisture along the cable length.
The outer jacket is the first line of defense for waterproof cables, so its construction and materials are critical factors. However, the popular manufacturing process of overmolding offers a superior level of protection essential to optimal safety and performance.
Using sophisticated injection-molding machines, custom overmolding is a popular manufacturing process that, when applied to cable assemblies, adds a protective layer over wires, cables, and components to create a single, seamless piece and provide a number of desirable benefits. PVC is one of the most popular overmolding materials due to its excellent durability, moisture resistance, and flexibility.
During the overmolding process, cable assemblies are placed within mold cavities where hot liquid overlay material is injected at a high degree of pressure. The overmolding fluid adheres to the assembly and is allowed to cool, eventually giving the product an extra layer and the advantages that come with it, such as greater ingress protection, mechanical strain relief (which also helps with water protection), and the ability to add caps, attachments, and logos.
Combining high-quality off-the-shelf cabling with overmolding, CAI offers extremely reliable and cost-effective waterproof cable solutions customized to your volume and application needs. For over 35 years, CAI has been creating superior electrical products, from cable assemblies to wire harnesses, for businesses across nearly every industry. That includes those needed for demanding environments where water, temperatures, chemicals, and more can impact performance and safety. Reach out today for expert help with your next big project.