Exploring 12 Common Sensor Types & Their Impact on Performance, Safety, & Convenience From kitchen appliances to vehicles, electronic sensors have long been essential components inside the devices we enjoy as a society. Sensors are used to detect...
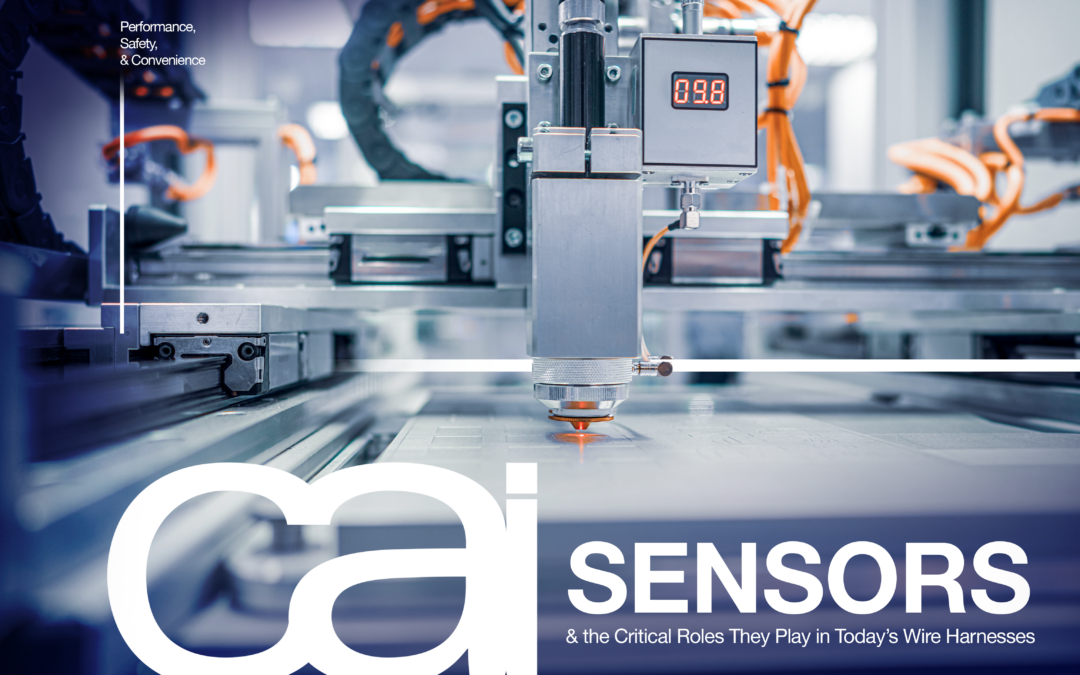
Exploring 12 Common Sensor Types & Their Impact on Performance, Safety, & Convenience From kitchen appliances to vehicles, electronic sensors have long been essential components inside the devices we enjoy as a society. Sensors are used to detect...
Why CAI is Your Wire Harness Cost Savings Solution In the increasingly competitive world of modern manufacturing, wire harnesses are essential components across a broad range of industries, from automotive and aerospace to industrial machinery and consumer...
Intricate Wire Harnesses Require Custom Solutions From Trusted Experts Used in countless electrical applications, wire harnesses come in all shapes, sizes, and complexities. While a “simple” wire harness organizes a handful of wires into a bundle for basic...
Ensuring Optimal Safety in Wire Harness Design The ability to control and utilize electricity — for everything from lighting homes to powering cars — is easily one of history’s greatest achievements, leading to many of our modern conveniences. However, there...
Extreme Conditions Call for Extra Consideration in Wire Harness Manufacturing Wire harnesses must be carefully crafted in order to effectively supply power and data to the machines and devices we use in our homes and businesses every day. The same is true for...
Whether we’re heading to work, a friend’s house, or the store, it’s easy for us to take for granted that every time we get into our cars and trucks, we’re getting behind the wheel of a highly complex high-performance machine, trusting it not only to get us to our destination, but to do it as safely and efficiently as possible.
We put a lot of faith in the manufacturers who make them and also the components inside them to perform reliably. This includes the wiring system throughout the vehicle which supplies the essential power and data. Without these, vehicles would fail to run.
Resembling the human body’s circulatory system, automotive wire harnesses are spread out throughout a vehicle, but instead of facilitating the movement of blood, they transport the power and data necessary for it to operate. The automotive wire harness is an assembly of connectors, cables, and terminals throughout the vehicle.
Often extending out from the instrumental panel to the front and rear of a vehicle, the complete automotive wiring harness is generally divided into several sections including the engine (ignition, starter, etc.), lighting, air conditioning, and auxiliary appliances.
Wire harnesses not only contribute to the car’s movement but also power important safety features like locks, sensors, gauges, and security systems, as well as comfort features like automatic windows. Unsurprisingly, automotive wiring systems are highly intricate.
According to Siemens, some modern vehicles contain nearly 40 different harnesses with approximately 700 connectors and over 3,000 wires. If disassembled and stretched into a continuous line, these wires would exceed 2.5 miles in length and weigh roughly 132 pounds.
In order to ensure optimal performance and reliability, CAI — a trusted custom wire harness manufacturer for over 35 years — considers a number of key factors when designing automotive wire harnesses, including:
Simple physics holds that the lighter the vehicle, the better, especially when it comes to key factors like speed, handling, and fuel efficiency. During the design phase, the overall weight of the harnesses is an important consideration, so manufacturers have to pick materials carefully. They also do all they can to minimize cable lengths whenever possible, because the weight can add up quickly.
The materials used in the harness must meet legal requirements and industry standards. While most components can be wired with wire between 4- to 16-gauge, battery cables must be larger to handle the starter’s heavy amperage load. Meanwhile, while most automotive applications use copper wire, aluminum has been replacing copper in vehicles to help lower weight. Its lower price tag helps overall costs too. And when it comes to joining methods, crimping is the preferred one for attaching wires to terminals due to its strength and reliability.
Due to harsh conditions such as extreme temperatures, moisture, vibration, and heavy power loads, durability is essential when considering everything from the jacket to the insulation to the conductors. Not only do wires and components need protection from external threats in order to perform reliably for long periods of time, but the rest of the vehicle needs protection from the flow of electricity and electromagnetic interference. Connectors and insulation have to feature special attributes to guard against things like vibration and heat. The most widely used insulations on automobiles are PVC and cross-linked polyethylene (XLPE). This all plays a part in the safety of harnesses as well.
Safety and durability go hand in hand because the more vulnerable wire harnesses are to their environments, the less safe they are. Inadequate protection can lead to dangerous situations such as on-road driving failure, equipment damage, or fire from a short circuit. Manufacturers often enhance protection through special assembly processes such as heat shrink tubing and applying fire-resistant tape and other materials. Because safety is so important, automotive wire harnesses undergo rigorous testing as well as extreme care and diligence during the design, production, and installation stages.
For ease of installation and future access, a key factor in the design of a custom wire harness is how it will be routed through the vehicle, such as through the chassis or between the cabin and engine bay. Proper routing optimizes compact spacing and also plays a role in other considerations including safety and repairs.
Before being tied (or “harnessed”) together, wrapped in protective covering, and installed in a vehicle, the wires, connectors, and components are laid out in their respective positions.
They are also properly labeled or color-coded to organize and differentiate parts from each other. Furthermore, knowing the current rating of every wire and clearly labeling them is a key step to avoid dangerous overloading.
When it comes to repairs, mechanics often rely on the technical manuals to know exactly which parts to use. As with all mass-produced products, uniformity is key to ensure expected performance and make repairs.
Today’s cars and trucks are obviously more advanced than ever, and therefore require even more intricate attention to their wiring, especially when it comes to EVs (electric vehicles). The more advanced vehicles become, the more specialized and intricate automotive wire harnesses will become. CAI has proven experience in custom and specialty vehicle harnessing solutions and is an ideal partner in design-build creativity for yielding system and material durability!
No matter the volume or the industry, CAI can handle all your custom wire harness and cable assembly needs from automotive and medical to military and aerospace. Get in touch with CAI today for expert help bringing your electrical products to life.