Exploring 12 Common Sensor Types & Their Impact on Performance, Safety, & Convenience From kitchen appliances to vehicles, electronic sensors have long been essential components inside the devices we enjoy as a society. Sensors are used to detect...
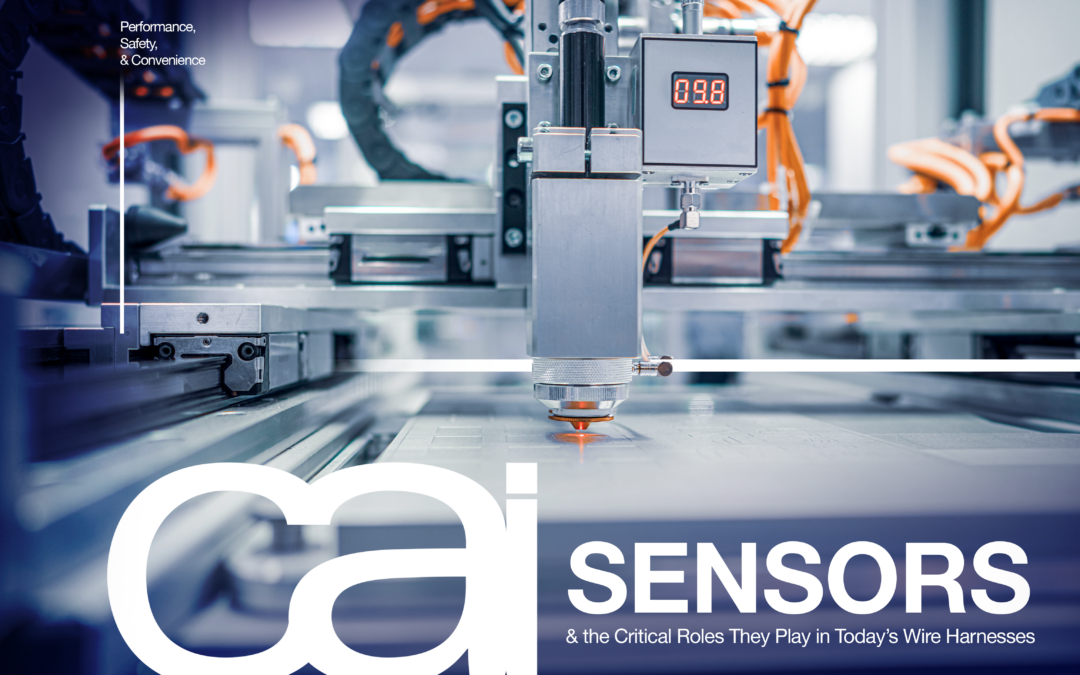
Exploring 12 Common Sensor Types & Their Impact on Performance, Safety, & Convenience From kitchen appliances to vehicles, electronic sensors have long been essential components inside the devices we enjoy as a society. Sensors are used to detect...
Why CAI is Your Wire Harness Cost Savings Solution In the increasingly competitive world of modern manufacturing, wire harnesses are essential components across a broad range of industries, from automotive and aerospace to industrial machinery and consumer...
Intricate Wire Harnesses Require Custom Solutions From Trusted Experts Used in countless electrical applications, wire harnesses come in all shapes, sizes, and complexities. While a “simple” wire harness organizes a handful of wires into a bundle for basic...
Ensuring Optimal Safety in Wire Harness Design The ability to control and utilize electricity — for everything from lighting homes to powering cars — is easily one of history’s greatest achievements, leading to many of our modern conveniences. However, there...
Extreme Conditions Call for Extra Consideration in Wire Harness Manufacturing Wire harnesses must be carefully crafted in order to effectively supply power and data to the machines and devices we use in our homes and businesses every day. The same is true for...
When you need to outsource the manufacturing of custom wire harnesses, cable assemblies, or other electrical components for your project and want someone who can handle it all — from design to delivery — you’ll need a trusted turnkey manufacturer like CAI to ensure your final product and overall experience are of the highest standards.
With your money, time, and project’s ultimate success on the line, choosing the right turnkey manufacturer from the get-go is of the utmost importance, but it’s not easy unless you know what to look for. This takes asking all the right questions and moving forward only when you get the right answers.
What follows are five of the most important questions you should be asking of your potential manufacturing partner. While you can often get the answers to most of these questions by perusing their website, it always helps to reach out directly to make sure they can check all the boxes for what you need from your manufacturer.
Considering the complex processes, skills, and precision required to create top-quality electrical products, proven experience is a critical factor. You’ll need a business who is known for meeting and exceeding client expectations time after time. Likewise, you don’t want to settle for an inferior one who may overestimate their abilities or cut corners.
For over 35 years, CAI has served countless satisfied clients around the globe with the highest quality of custom electrical systems and components. Although such proven expertise and experience often comes with premium prices, CAI still does all they can to find the perfect cost-effective solutions for their clients.
A turnkey manufacturer should be able to handle all aspects of the process, providing all manufacturing and supply chain services, including design, fabrication, installation, delivery, and aftermarket support. They should also have and help you choose the perfect materials, tools, technology, and services to meet your unique needs and specifications.
Able to handle volumes of all sizes, CAI offers a wide variety of essential solutions, including:
For more information about what CAI offers — including equipment (number of units/stations), PCB standards, and more — click here.
Electrical components like cable assemblies, wire harnesses, and PCBAs typically must adhere to specific industry performance and safety requirements. When choosing a manufacturer, you have to make sure they are familiar with the standards and regulations and have done similar work for your industry and application.
While there are niche manufacturers who only specialize in certain areas, it’s optimal to get one that has experience working with multiple different ones. Those with experience across many industries are more likely to have encountered a wider range of challenges. They also tend to offer more outside-the-box solutions when needed to save time and money or overcome any obstacles that may arise.
CAI has worked with businesses of all shapes and sizes in practically every industry, including:
For optimal performance, durability, and safety of your finished product, it must undergo thorough testing and quality control at critical points in the manufacturing process. The best outsourcing partner will put your product to the test, analyzing everything from electrical performance and mechanical strength to how it stands up to environmental conditions.
From the prototyping stage to post-production testing, CAI is committed to rigorous testing of the products they manufacture and offer a vast array of testing capabilities, including:
Wire Harness & Cable Assembly Testing
PCBA Testing
Apart from their experience and capabilities, it’s also important to verify that the manufacturer is qualified to handle your project and that they hold themselves to the industry’s highest quality and safety standards.
CAI is a member of the Wire Harness Manufacturer’s Association — the only trade association exclusively representing the cable and wire harness manufacturing industry including manufacturers, their suppliers, and customers. They also adhere to the standards from SAE International — a global association of more than 128,000 engineers and related technical experts in the aerospace, automotive, and commercial-vehicle industries.
Additionally, CAI is experienced with UL certified processing requirements which assure UL’s safety standards. They are also well versed and compliant with industry standards such as ISO9001:2015 (which means that they have put in place effective processes and trained staff to deliver flawless products or services time after time) and IPC-A-610, otherwise known as Acceptability of Electronic Assemblies (which sets the standard for what is or is not acceptable during assembly of printed circuit boards).
With decades of experience and all the turnkey capabilities and qualifications you need, CAI is the best outsourcing choice for your electrical component manufacturing project. Contact us today for answers to all your questions and more insight into what we can do for you!